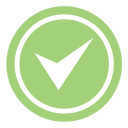
Validity
This Executive Order approved the specified parts on on November 14, 1986.
As of Tuesday, June 24th, 2025 this Executive Order has not been overturned or superceeded.
This Executive Order approved the specified parts on on November 14, 1986.
As of Tuesday, June 24th, 2025 this Executive Order has not been overturned or superceeded.
Part Number | Models | Modification |
---|---|---|
No. ATS 6.9L | 1983-1987 model-year Ford Motor Company heavy-duty vehicles powered by a 6.9 liter Navistar International heavy duty diesel engine. | Modifications to the OEM emission-related parts due to the installation of the turbocharger kit include replacement of the air cleaner assembly and replacement of the OEM exhaust system with a 3" diameter exhaust system. |